The new standards will increase the demands and requirements placed on the brake pads, writes Christian Stolz
The new Euro 7 standards came into effect on 28 May 2024. For the first time ever, brake emissions have come into focus, but what does that mean for manufacturers and the wider automotive industry? In the simplest of terms, manufacturers selling into the EU will need to prioritise finding solutions that will adhere to the legislation and reduce their environmental impact.
Euro 7 will require that the abrasion of brakes be severely limited in the future, increasing the demands and requirements placed on the brake pads. The draft stipulates that particulate emissions from brake abrasion (PM10) may not exceed 3-11 mg per kilometre per vehicle, depending on the vehicle class and drive type. While the industry has made significant progress in reducing vehicle emissions, particularly from the pollution caused by the combustion tract, pressure is mounting on manufacturers to go even further.
However, when it comes to brake friction formulas, it’s not as simple as just removing one raw material and replacing it with another. This was evident when removing asbestos or copper. Each material needs to have the right properties and integrity to work in harmony together to perform as expected. Often, you may need to replace one raw material with several to achieve the same performance as before.
When it comes to brake friction formulas, it’s not as simple as just removing one raw material and replacing it with another
So, when it comes to limiting brake emissions, it is not quite so straightforward. It is often assumed that most of the abrasion comes from the brake pad but in fact, around 80% of the emissions or dust in the rim is abrasion from the disc. The amount of disc material removed depends on the selected friction material formulation of the brake pad. This alone is no longer sufficient to achieve the Euro 7 limits, resulting in new, more unconventional friction concepts being required.
New concepts
All industry players are now working to find concepts that comply with Euro 7 emissions. One idea is to capture the brake dust after it is generated using filters. However, this would result in OEMs redesigning their brake systems to include a filter. It will also mean additional parts for the vehicle, which will contribute to more weight as well as extra maintenance to clean, replace and dispose of collected brake dust emissions.
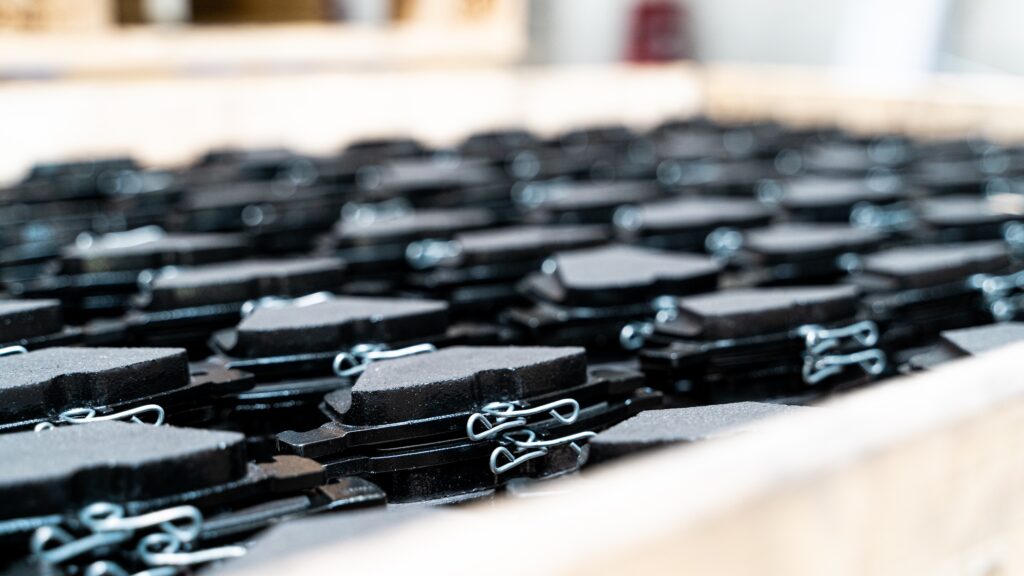
Another concept is to tackle the emissions and the formation of brake dust directly at the source, namely at the brake pad and the brake disc by carefully formulating a coordinated friction pairing. This is currently the most promising route for reducing emissions by utilising a hard material coated grey cast iron disc in combination with a tailor-made friction material mixture developed specifically for the vehicle application.
To achieve the right application for each vehicle’s braking system, the brake manufacturer must continuously monitor the effects on performance, durability, and cost-effectiveness of a friction pairing. The experts on the test bench, and on the test track, must also continuously review the comfort and noise behaviour.
The tribological and NVH (noise, vibration, harshness) behaviour of coated grey cast iron discs will be essential. Resolving this trade-off of low abrasion despite maximum performance and tackling emissions at the root where they arise will only be achieved by specialists that develop materials themselves and are involved in corresponding projects at an early stage with the vehicle manufacturer.
Investment
In addition to the technical challenges generated by the Euro 7 standards, the new regulation will also create additional economic problems for some industry players. The effort required to provide appropriate solutions for Euro 7 in the aftermarket is significant. The investment for a test bench is approximately €1.5m and the total running time for one material is around 27 hours. This includes six cycles, each of which simulates 303 braking operations over a distance of 192km. With this in mind, it is clear it will become ever more difficult for low-cost standard compounds to survive in the European market in the wake of increasing requirements.
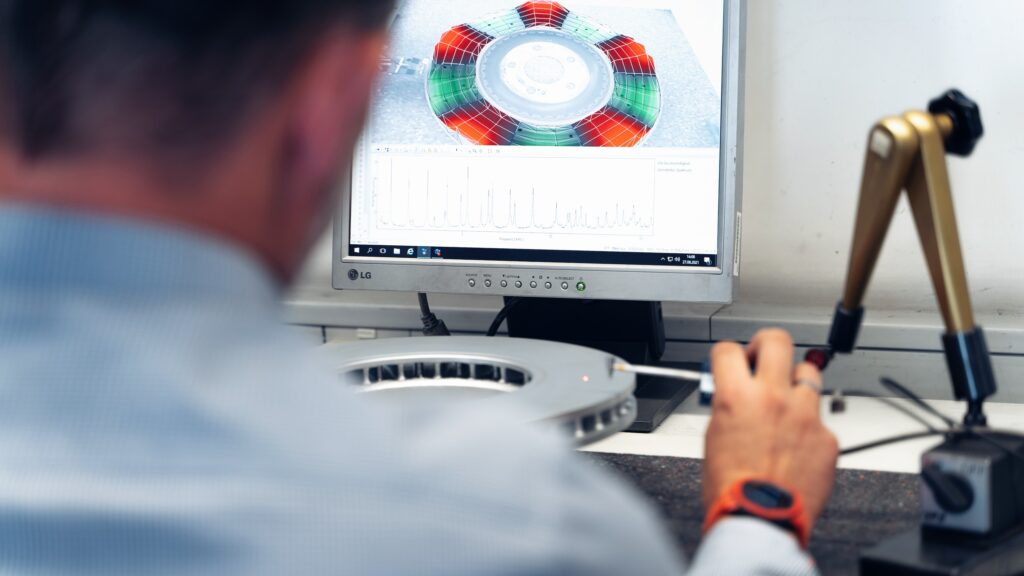
Investment into developing a new concept is significant and requires a level of extensive knowledge and experience. That’s why the automotive industry needs expert partners who understand the complex brake system and offer the appropriate testing and development capacities—and not just in series production.
The new standards will initially only apply to original equipment (OE) products but will undoubtedly filter into the independent aftermarket (IAM), most likely via the ECE R90 directive, making the Euro 7 standards relevant for both original equipment and the aftermarket. In the future, aftermarket brake pads and brake discs will not only have to correspond to the original products in terms of performance and braking behaviour, as has been the case in the past, but they will also have to comply with the emission limits.
The reduced wear behaviour will mean the replacement intervals will no longer be determined by the achievement of the wear limit, as was previously the case, but by time intervals
The Euro 7 homologation requirements for the independent aftermarket are still under development but are expected soon, considering transition periods too. This will presumably give the aftermarket time to familiarise itself with the different solutions offered by vehicle manufacturers, and to develop and homologate appropriate products accordingly. As a rule, at least one to two years pass before new vehicles arrive at the independent workshops or until pads or discs must be replaced. If an earlier replacement is necessary, for example, in the case of frequent driving, before the end of the transition period, the original parts are alternatively available at the authorised workshop to restore them to their original condition.
Essentially, the reduced wear behaviour will mean the replacement intervals will no longer be determined by the achievement of the wear limit, as was previously the case, but by time intervals. This can be thought of as a use-by date, as the components age due to environmental and operating conditions, and then must be replaced accordingly.
The recent approvals from the EU Parliament and EU Council were key milestones in determining the next steps and requirements for the new Euro 7 standards. The transition period allows some additional time to find the right solution that meets the legal requirements. But brakes are a critical part of the vehicle’s overall safety, so while lowering emissions is important, it should never be at the detriment of the braking performance.
About the author: Christian Stolz is Vice President R&D OE at TMD Friction, a global brake manufacturer for the Textar, Mintex, Don, Pagid, Cobreq, and Bendix braking brands